Aldeno Technology Co., Ltd. has been focusing on high-reliability electronic assembly manufacturing services for more than ten years, providing one-stop electronic manufacturing services such as PCB manufacturing, electronic component procurement, SMT placement, DIP plug-in soldering, PCBA testing, three-proof paint coating, electronic sealing and filling, and PCBA low-voltage injection moulding and overmoulding.
We are equipped with an engineering team of electronic engineers, QE engineers and structural engineers with more than ten years of experience in the electronics industry to ensure reliable quality. In order to reduce customer procurement and supply chain management costs, we have set up a professional electronic components procurement team, including electronic procurement engineers, BOM engineers, etc., and with domestic and foreign well-known electronic components channel business and the original factory, to establish strategic partnerships.
Aldeno Technology has the whole process of PCBA manufacturing equipment, including automatic solder paste printing machine, SMT mounter, ten temperature zone reflow soldering, nitrogen vacuum reflow soldering, wave soldering, three-proof paint spraying line, AOI optical inspection, X-ray ray inspection, FAI first piece inspection, SPI solder paste inspection, ICT circuit inspection, FCT function checking and other equipment.
PCBA Process
- We provide PCBA full-process professional services, from the procurement of electronic components to semi-products, finished products, are able to accurately docking customer needs, and go all out to the customer‘s products from the programme, drawings to the realization of the finished PCBA product.
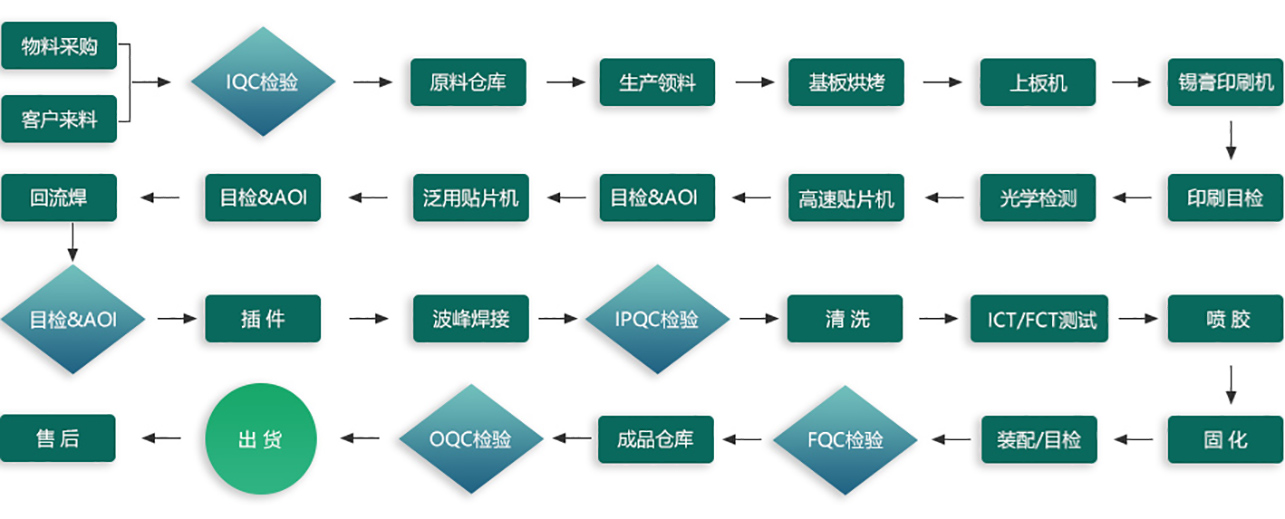
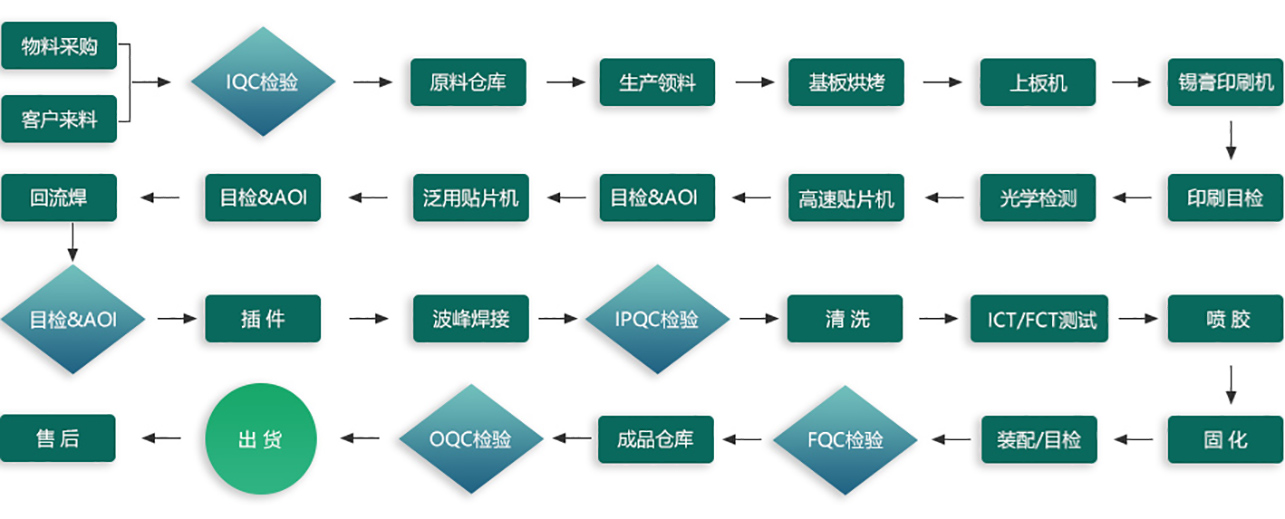
PCBA manufacturing capacity table
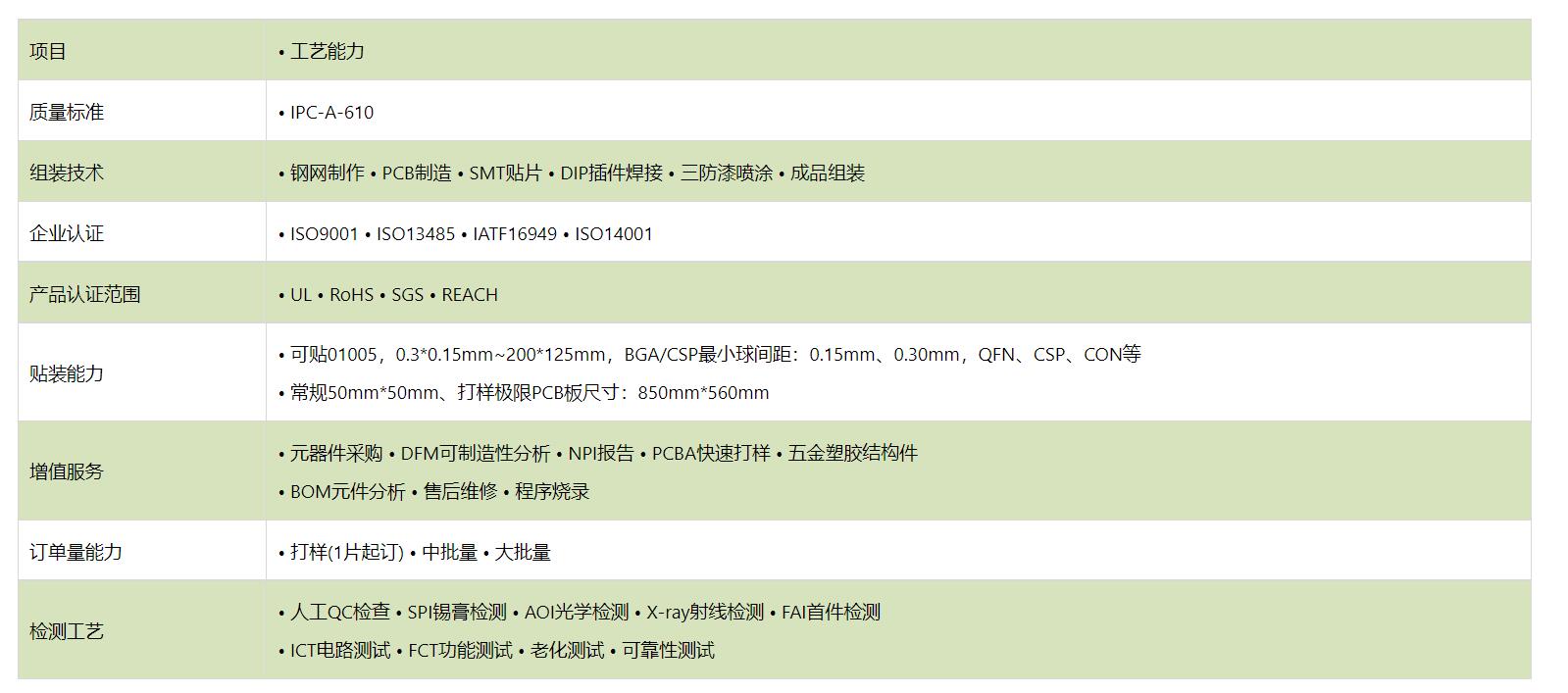
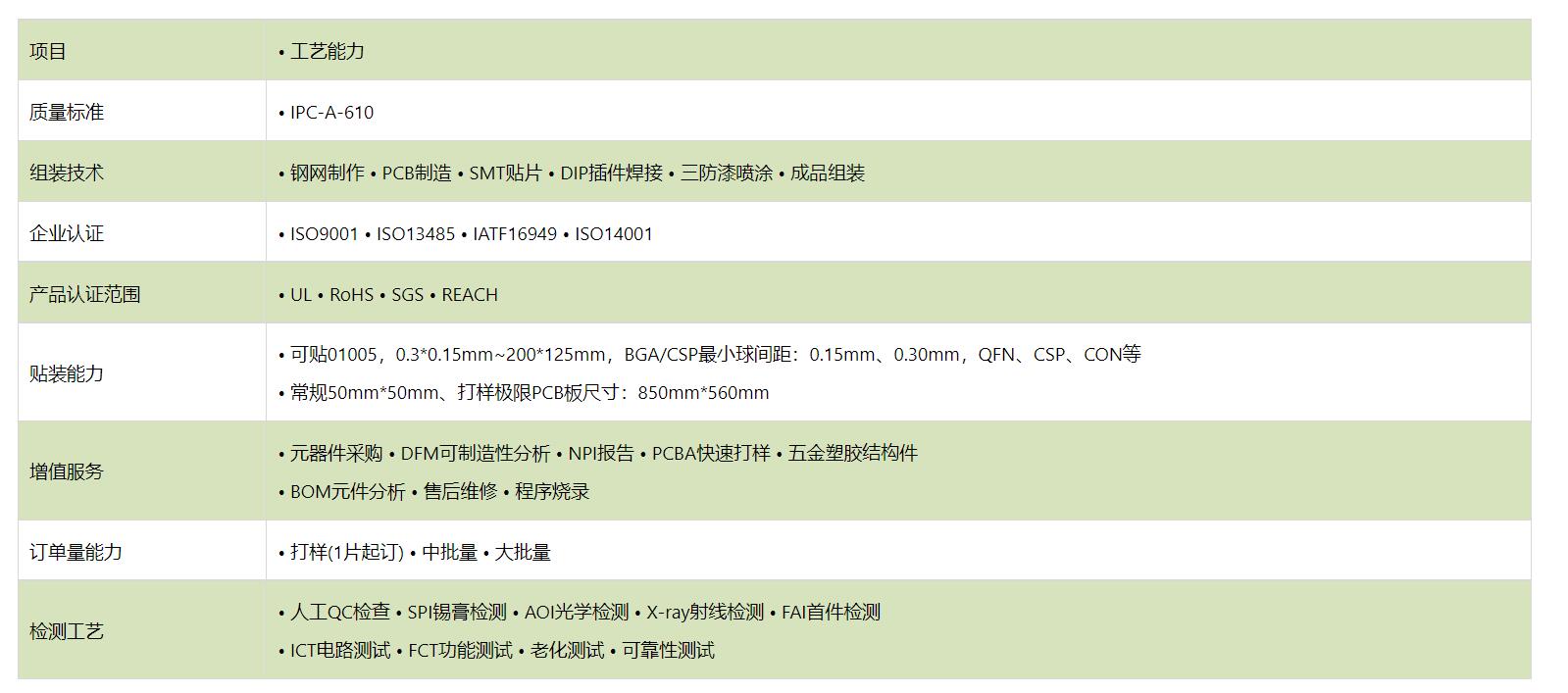
Sample display
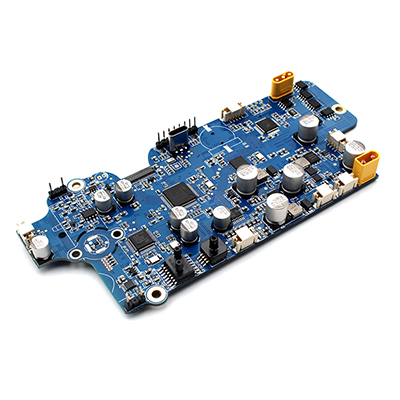
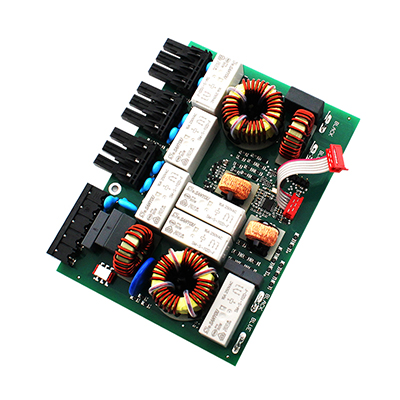
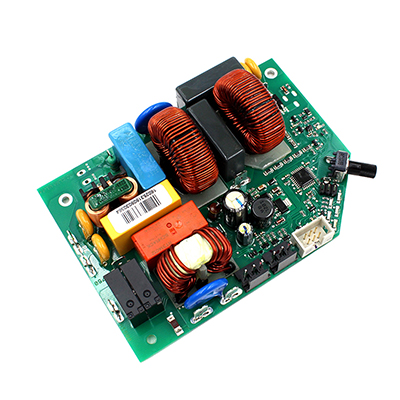
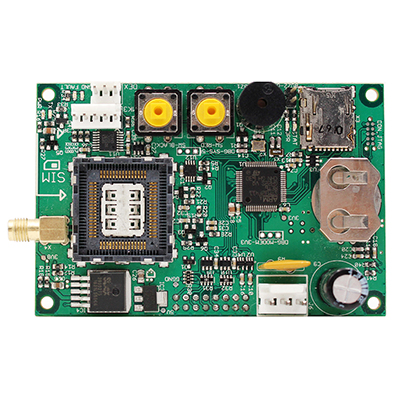
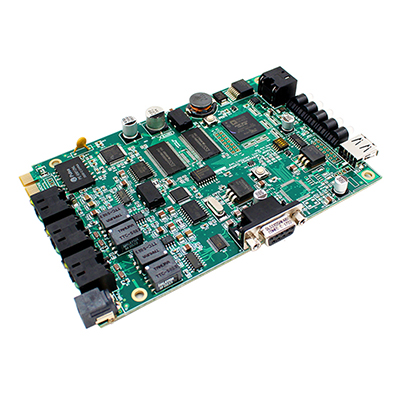
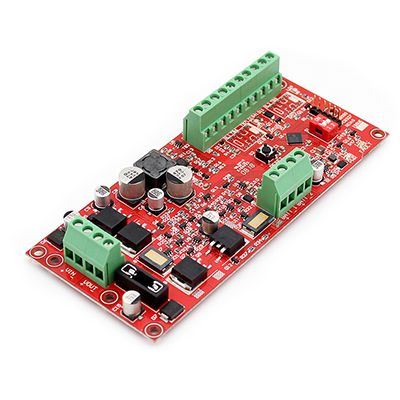
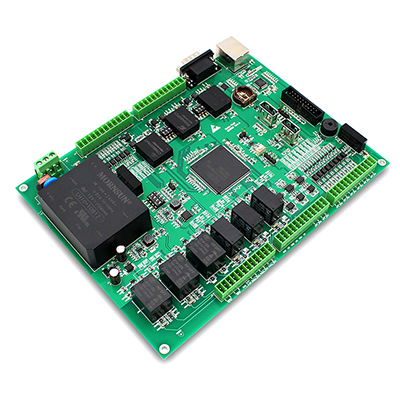
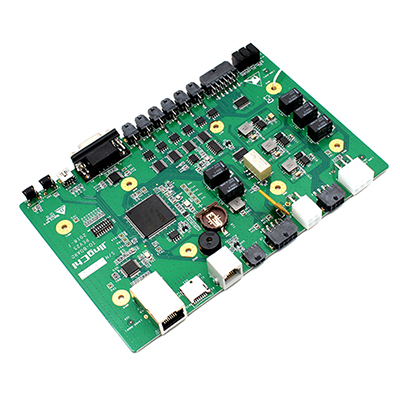
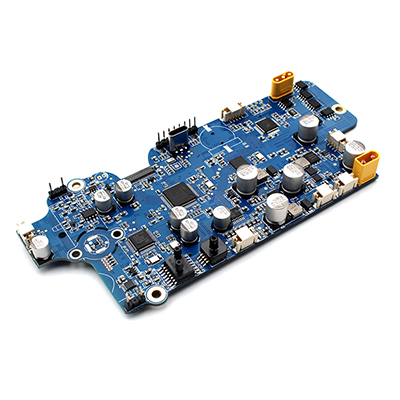
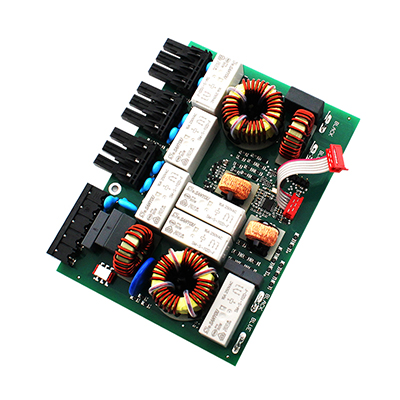
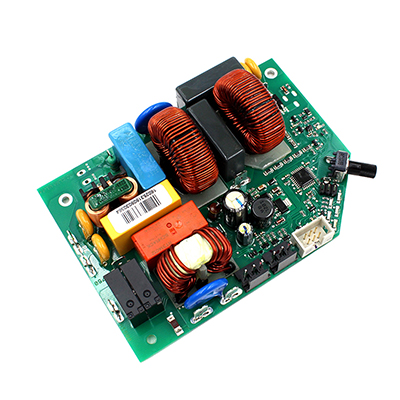
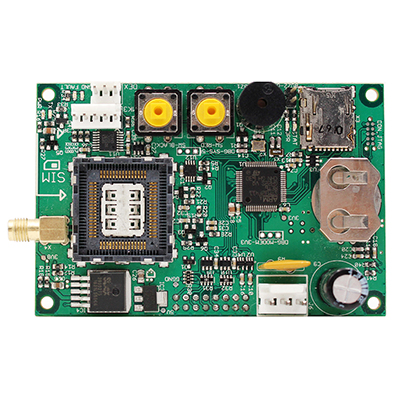
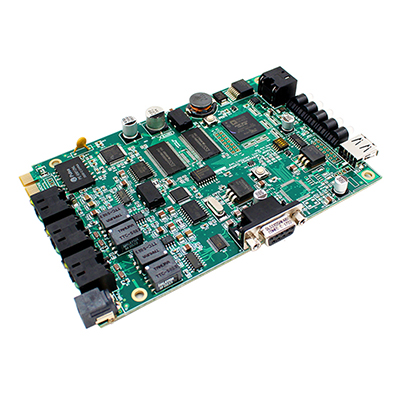
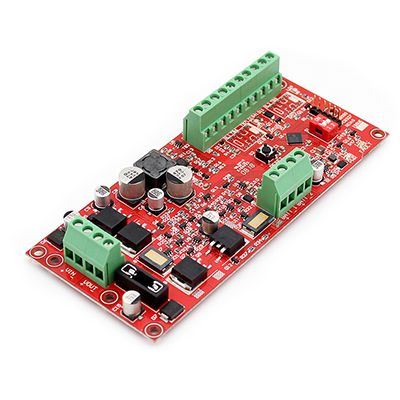
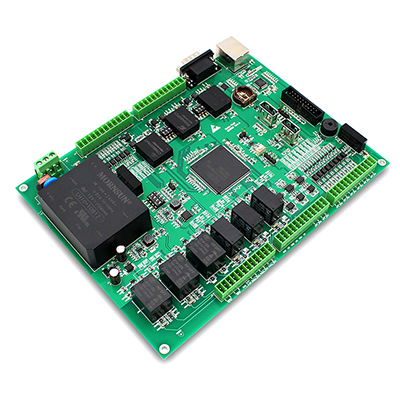
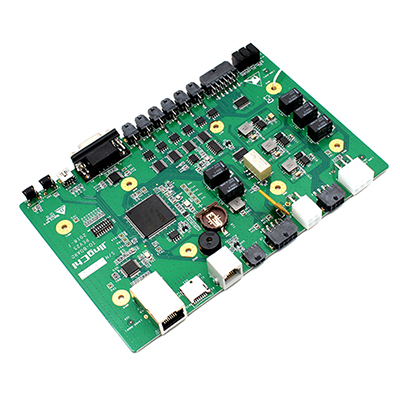
DIP Insertion Soldering
- Our DIP plug-in process capability
- Plug-in AOI for component error, leakage and reverse detection, strict control of the DIP through rate.
- Skilled soldering irons under strict training, soldering speed and quality can be controlled.
- According to the state of the circuit board, equipped with independent identification of the temporary storage area around the wire: to be inserted, to be repaired, to be QC inspection, defective products, to be QA inspection, etc., to avoid the emergence of mixed boards.
- Strict IPQC and QA LOT sampling standards to ensure the reliability of the DIP process.


- DIP insertion processing equipment
- Insertion line: 2 lines
- Insertion AOI: check the defective items of inserted components and solder joints.
- Wave soldering x: 2 sets
- Wave soldering x: 2 sets Post-soldering pulling line x 24 stations
- Board washer x 1 set
- DIP insertion processing is a part of PCBA electronic processing process, manual work is relatively more, for the management to put forward higher requirements. Through the implementation of a set of perfect quality management system ISO9001:2015, ISO14001, ISO13485, IATF16949, and equipped with constantly upgrading automation equipment (such as automatic depaneling machine, automatic dispenser, automatic spot welder, etc.), jigs and fixtures, etc., which makes our DIP processing service consistency and reliability is extremely high, and win the praise of customers.
DIP plug-in processing process can be generally divided into: component moulding processing → plug-in → over wave soldering → component cutting foot → complementary welding (post-soldering) → washing board → function test
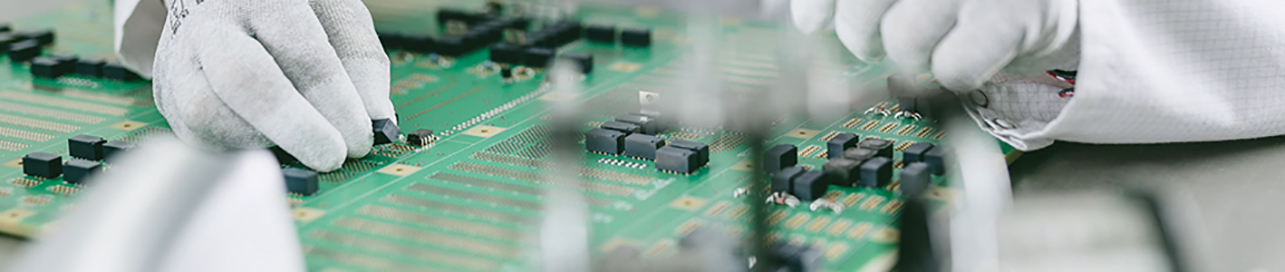
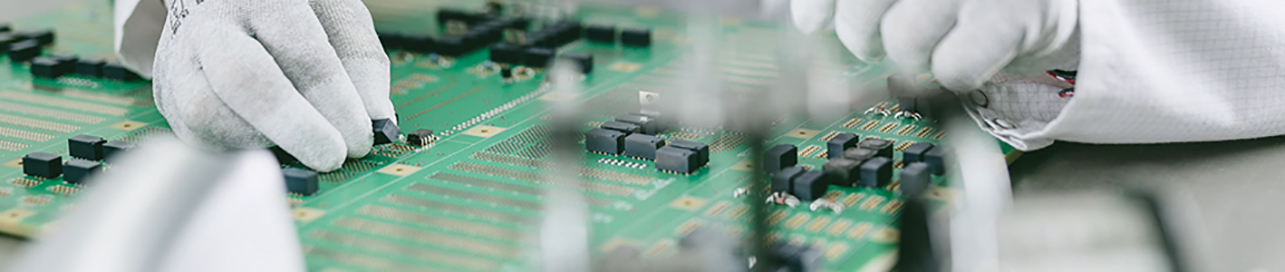
Three-proof paint spraying
Our company is equipped with professional technical engineers, adjusting the machine procedures to ensure that the board surface spraying uniformity, excellent results!
- Three-proof paint is a specially formulated coating used to protect circuit boards and related equipment from environmental erosion. Three-proof paint has good resistance to high and low temperatures; its curing into a transparent protective film, with superior insulation, moisture-proof, leakage-proof, shock-proof, dust-proof, corrosion-proof, anti-aging, corona resistance and other properties. In order to meet the customer‘s products for humidity, temperature, corrosive and other harsh environments and configure the needs of the application, our company specialised in configuring a three-proof paint spraying production line, including a three-proof paint spraying equipment, UV testing, baking, including a fully automatic one-stop mode. We will be happy to serve you!
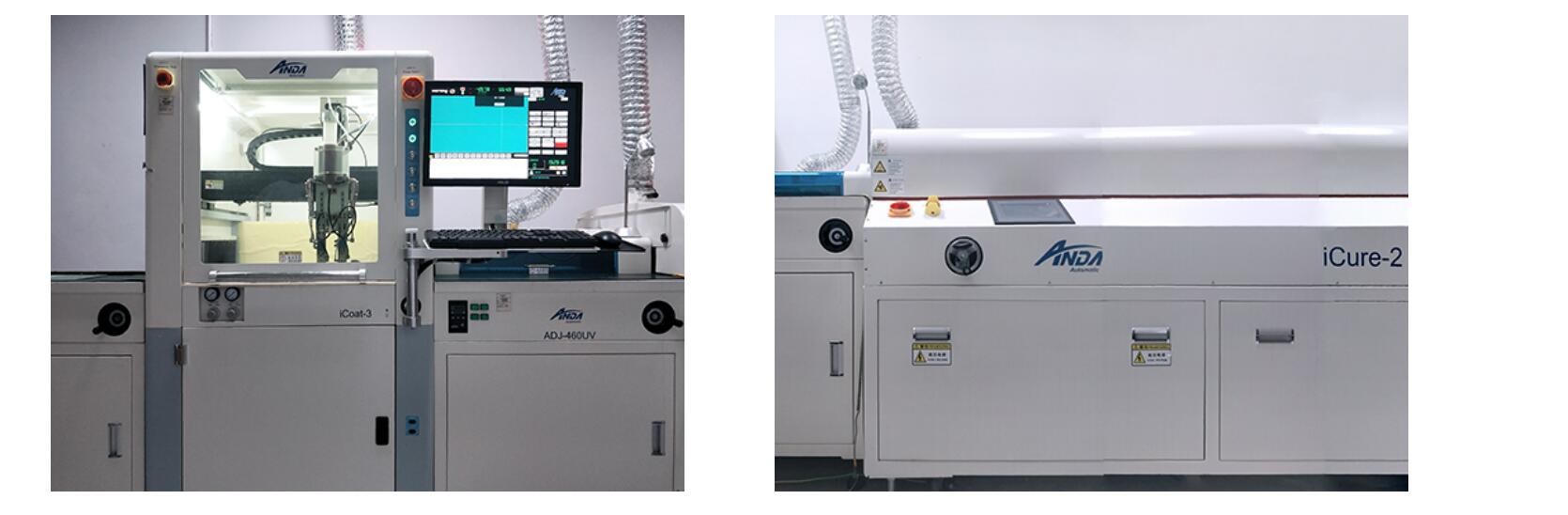
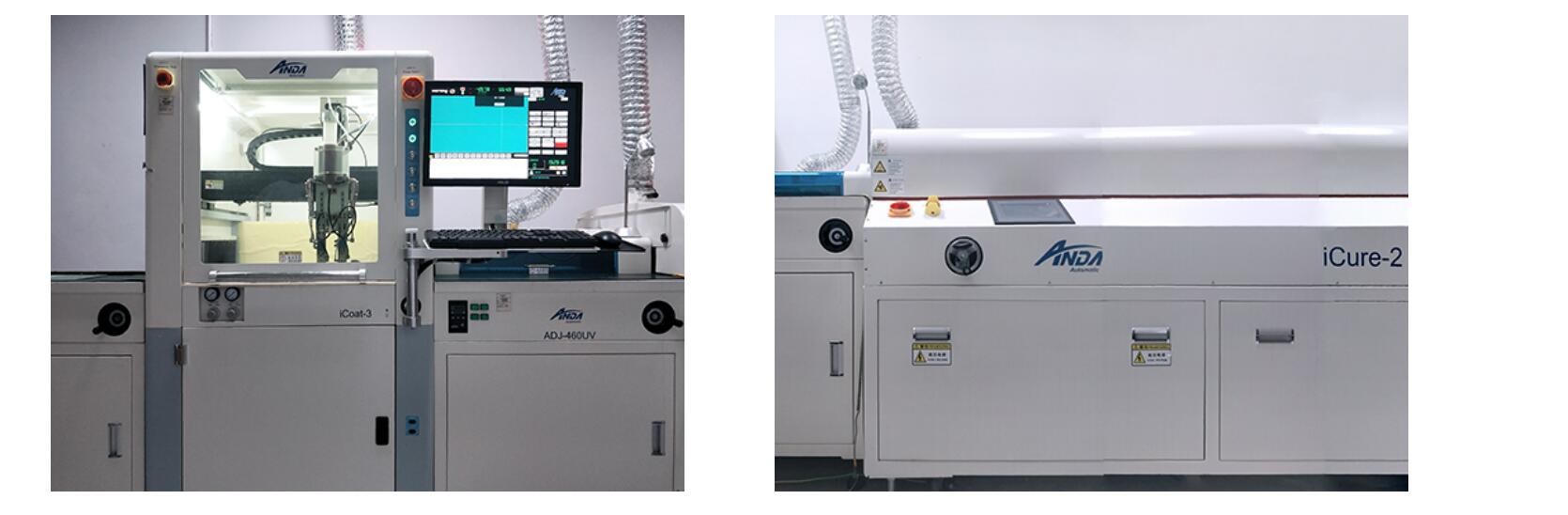
Advantages of three-proof paint processing
- Traditional manual painting will have poor consistency, quality accidents (such as three-proof paint penetration into the LCD screen, socket, etc.), uneven thickness, three-proof paint mixed with impurities. The use of professional three-proof paint spraying production line can effectively avoid these defects, with the advantages of fast speed, high reliability, one-stop baking and curing.
Supported types of three-proof paint processing
- Large size PCBA boards, such as 550mm*470mm, etc.
- Provide matching PCBA board carrier, effectively ensure the uniformity of edge spraying.
- Support dense PCBA boards with many high components.
- Sector spraying and dot-pin spraying can cover all kinds of component surfaces.
- According to the actual needs of customers, you can selectively avoid certain components, such as connectors, antennas, Wifi modules, heat sinks and so on.
- Support double-sided coating and baking
- Fully automatic equipment, average spraying time per board within 0.5~3 minutes
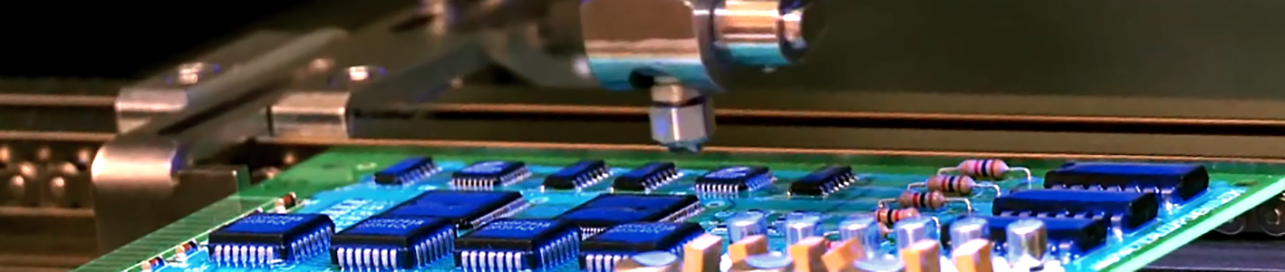
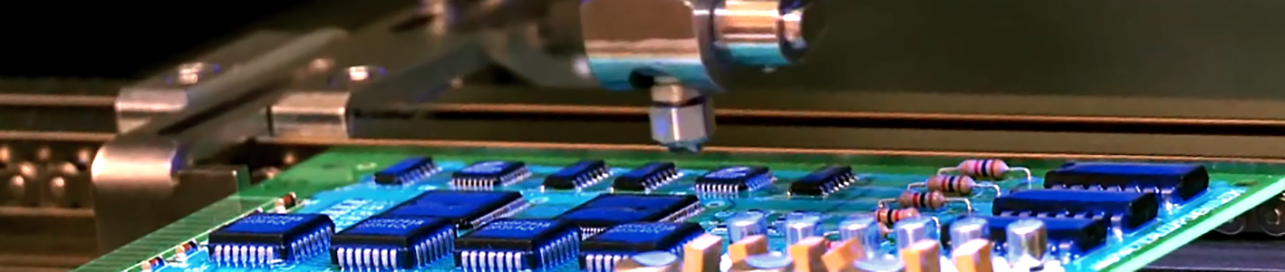
Quality Control
- For potential defects or non-conformities, etc., analyse and carry out appropriate error-proofing design and quality control through the use of tools such as tests, simulations, data analysis, QC techniques, etc., and propose preventive action plans.
- For the bad or non-conformity has occurred, the problem solving team to re-assess and approve the revision of the relevant technology, quality standards or improve the level of technology or design, etc., to confirm the quality system related to all products or processes whether there are similar problems and comprehensive prevention and proposed solutions.


[People]: From material procurement to product delivery, each link is equipped with quality personnel, including: incoming material inspection IQC, production inspection IPQC, finished product inspection OQC and so on. Production technology, management personnel have more than 5 years of manufacturing experience in the electronics industry, to solve problems more timely and effective.
Machine]: In order to meet the high and end quality requirements of customers, our company is equipped with high-end production equipment, but also equipped with sophisticated PCBA testing equipment, including testing equipment: X-ray, AOI, UV test bench, FCT equipment, etc., so that each piece of PCBA boards can withstand heavy testing.
Material]: With more than 6 years of experience in electronic components procurement procurement team, not only to achieve the order full BOM procurement, but also to maximise the protection of material quality. Especially with the formal component brand channel business and original factory cooperation, greatly enhance the price, delivery, quality and other advantages, such as: Arrow, Traders, Digi-Key, Litron and so on!
[System]: No matter material storage or semi-finished product, finished product storage are in accordance with the coding rules and entry standards, through the ERP system for data storage, in order to product quality traceability. Equipped with FAI first piece inspection system can significantly reduce the risk of wrong material, less material, but also to improve production efficiency.
Enterprise qualification:
- After inspection and evaluation by authoritative institutions, Gauto‘s products, processes and services comply with ISO9001, ISO13485, IATF16949, ISO14001, UL, SGS, RoHS and other authoritative certificates, and relevant certificates are issued, and Gauto has the ability to continuously and stably produce products in line with standard requirements.

